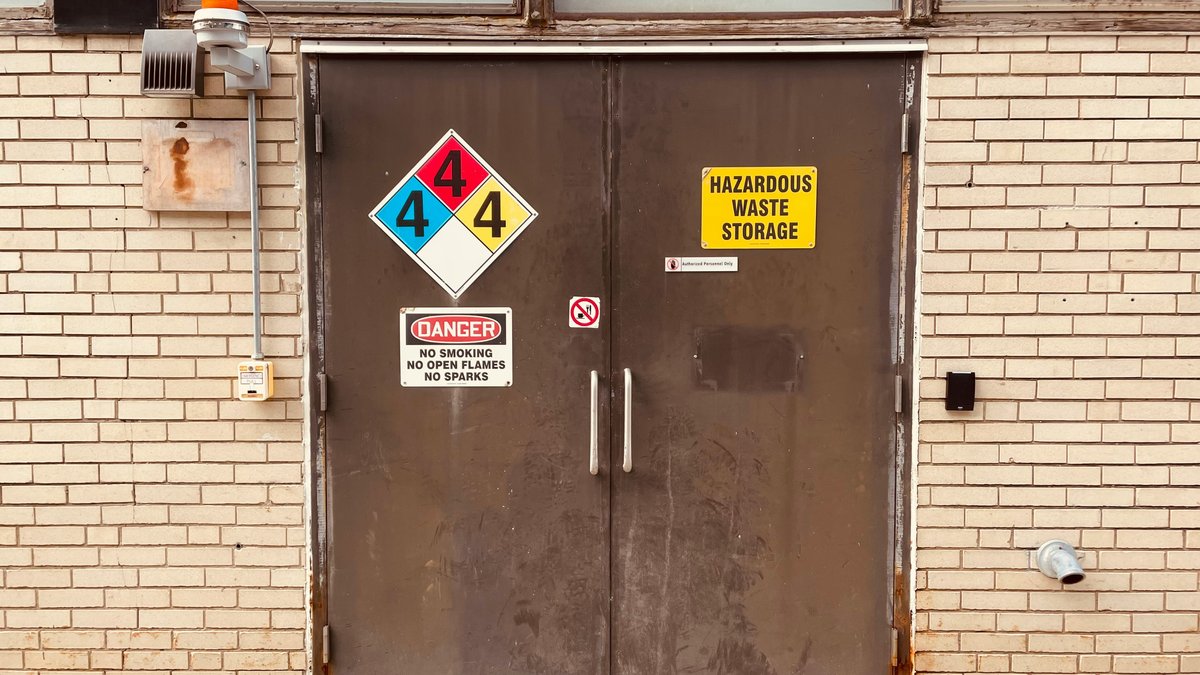
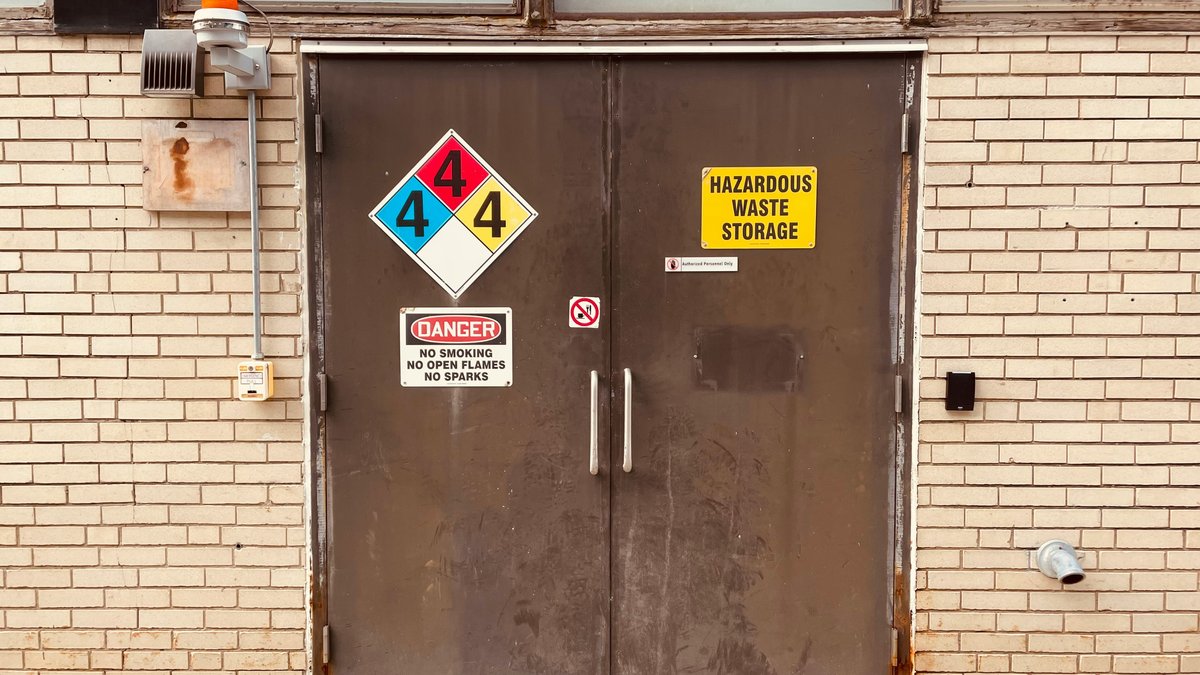
Navigating the world of chemical safety and OSHA compliance can be daunting. Safety Data Sheets (SDSs) are the cornerstone of hazard communication, but even seasoned professionals can fall prey to common SDS compliance mistakes. Ensuring accurate and accessible SDS information is critical for workplace safety. This post will highlight five frequent errors and provide actionable steps to ensure your workplace remains compliant and minimizes SDS risk management challenges.
- Outdated SDS Libraries
The Mistake: Relying on old or outdated SDSs. Chemical formulations change, and regulations evolve. Using outdated information can lead to serious safety hazards and compliance violations.
The Solution: Establish a routine system for reviewing and updating SDSs. Regular audits, vendor communication, and subscribing to industry updates can help keep your SDS library current. - Inadequate Employee Access
The Mistake: Storing SDSs in a location that’s difficult for employees to access during emergencies. Time is critical when dealing with chemical spills or exposures.
The Solution: SDSs should be readily available through multiple channels, including digital and physical copies. Implement mobile-friendly access points, QR codes, and ensure employees are trained to locate and interpret SDSs quickly. - Neglecting Secondary Container Labeling
The Mistake: Failing to properly label secondary containers with essential safety information. This oversight can lead to confusion and miscommunication about chemical hazards.
The Solution: Ensure that all secondary containers are labeled according to regulatory requirements. Use standardized labels that include hazard pictograms, precautionary statements, and chemical identifiers to avoid misinterpretation. - Poor Chemical Inventory Management
The Mistake: Not tracking chemical usage, storage, and disposal. This lack of oversight can lead to inaccurate SDS records and difficulty in complying with EPA reporting requirements.
The Solution: Implement a structured chemical inventory management system. Conduct regular reconciliations to ensure that SDS records align with the actual chemicals in use, and establish clear procedures for proper storage and disposal. - Ignoring Employee Training and Hazard Communication
The Mistake: Providing SDSs without adequately training employees on how to interpret and apply the information. Simply having SDSs on file is not enough.
The Solution: Conduct frequent training sessions focused on SDS interpretation, chemical safety, and emergency response. Ensure employees understand how to locate and use SDSs effectively to promote a safer work environment.
How SDS Manager Can Help
Managing SDS compliance manually can be time-consuming and prone to errors. SDS Manager provides an all-in-one solution for automatic SDS updates, digital access, compliant labeling, chemical inventory tracking, and employee training tools. With SDS Manager, you can streamline compliance, reduce risks, and ensure that your workforce always has access to the most up-to-date safety information.
Ready to simplify your SDS management? Schedule a free demo of SDS Manager today and take the first step toward a safer and more compliant workplace.