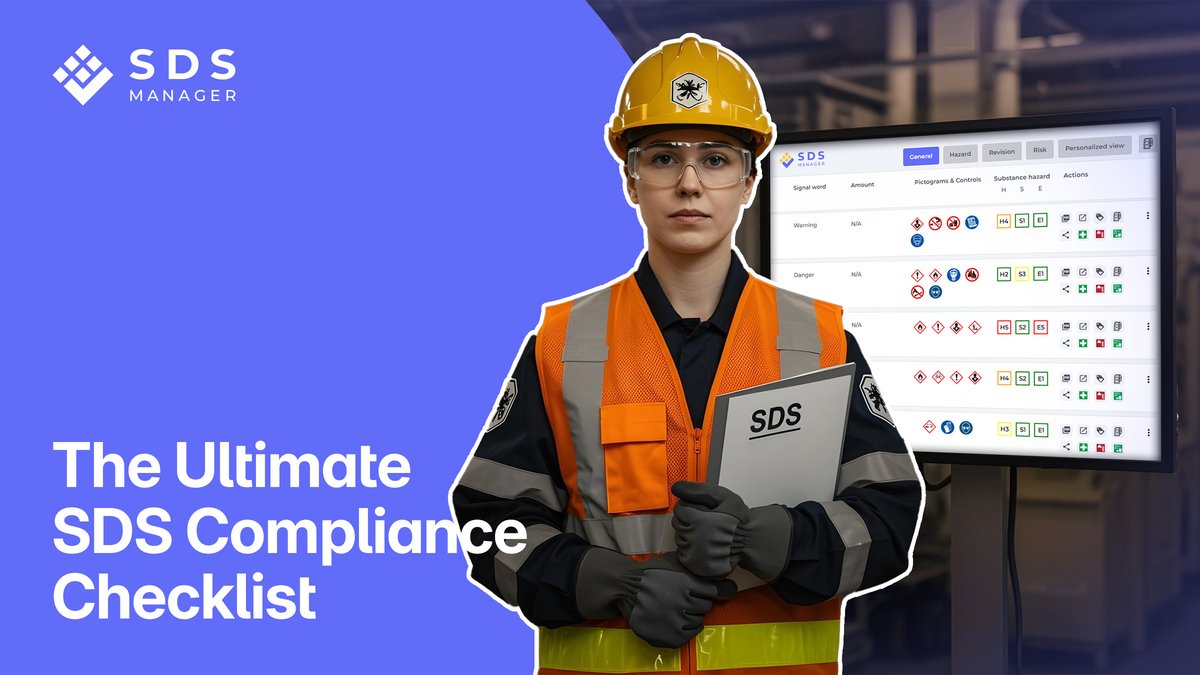
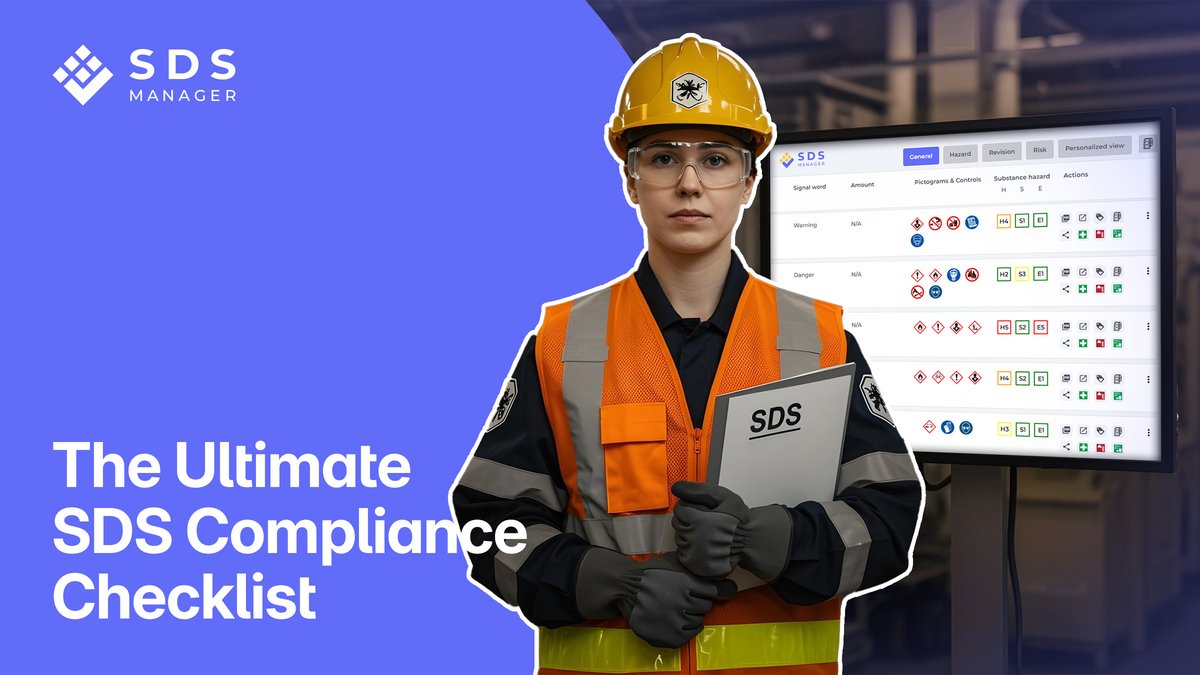
As regulations evolve and workplace safety expectations rise, the role of health and safety managers is more critical than ever. One of the foundational pillars of chemical safety is proper management of Safety Data Sheets (SDS). But staying compliant in 2025 isn’t just about collecting documents, it’s about making sure they’re accurate, accessible, and part of a proactive safety culture.
Why SDS Compliance Matters
An SDS (Safety Data Sheet) is more than just a document, it’s a critical tool for managing chemical hazards, protecting workers, and ensuring your workplace meets regulatory safety standards. Under the Control of Substances Hazardous to Health (COSHH) Regulations, UK employers must ensure that any hazardous substances in the workplace are supported by a current and accurate SDS. Proper SDS compliance helps protect employee health and safety, ensures legal obligations are met under COSHH and the Health and Safety at Work etc. Act 1974, and significantly reduces the risk of incidents or enforcement action by the Health and Safety Executive (HSE).
That’s why we’ve created the ultimate SDS compliance checklist. If you're responsible for chemical safety at your workplace, this is your roadmap to a safer, more compliant operation.
1. SDS Present for All Chemicals
Every hazardous chemical in your workplace, whether it's in use or in storage, must have an SDS. This is the first and most essential step in compliance. If a product arrives without one, contact the supplier immediately. You can also use our Free SDS search tool to find the SDS you need.
2. SDSs Are Up-To-Date
When a new SDS arrives, always check the revision date to ensure it reflects the most recent version. Regulations and formulations can change, so it’s important to confirm that you're working with the latest information. If the SDS is outdated or doesn’t show a clear revision date, reach out to your supplier for clarification or an updated version. Staying current supports compliance and protects your team.
3. Archived SDS Versions Stored
In the UK, it is essential to retain previous versions of Safety Data Sheets (SDS), particularly if a chemical product has changed over time or is no longer in use on-site. Under the Control of Substances Hazardous to Health Regulations (COSHH), employers must keep records of hazardous substances and potential employee exposures for at least 40 years. This requirement helps ensure that, in the event of a health concern, audit, or investigation, historical information about chemical hazards and exposures is readily available.
Archiving old SDS versions is a key part of compliance with COSHH and supports your duty of care to employees. These records can be stored securely in either physical form or, preferably, within a digital SDS management system to ensure they are easily accessible when needed by health and safety inspectors or occupational health professionals.
4. Correct Language
Safety Data Sheets (SDSs) must be provided in a language that your employees can understand. In the UK, this means that SDSs must be available in English. According to the Health and Safety Executive (HSE), it is the employer’s responsibility to ensure that safety information is clearly communicated to all workers. If your workforce includes employees who are not fluent in English, you should take additional steps such as providing translated SDSs to ensure everyone understands the hazards and safe handling procedures. Ensuring SDSs are comprehensible to all staff is not just good practice, but a legal requirement under UK law.
5. Digital or Physical Access Provided
SDSs must be easy to access for employees, especially at the point of use. Whether that means having printed copies near workstations or using a QR code system that links to digital files, the key is that workers can find and read the documents without delay. Accessibility is a core part of regulatory compliance.
6. Employee SDS Training Provided
Having SDSs on hand isn’t enough, employees must be trained to understand and use them. That includes recognizing hazard information, following safe handling procedures, and knowing what to do in an emergency. Training should be provided during onboarding, when new chemicals are introduced, and as part of regular safety refreshers.
7. Routine SDS Library Review
A best practice is to review your SDS collection every 6 to 12 months. This ensures that all documents are still up-to-date, and aligned with your chemical inventory. It also helps you identify outdated products or chemicals no longer in use. Regular reviews are one of the simplest ways to stay audit-ready. Be sure to mark the latest review date.
Your Go-To SDS Compliance Checklist
To simplify SDS compliance, we’ve created a comprehensive checklist. Whether you’re updating your chemical safety program or prepping for an audit, this checklist keeps you organized and compliant. Download the image below for quick reference.
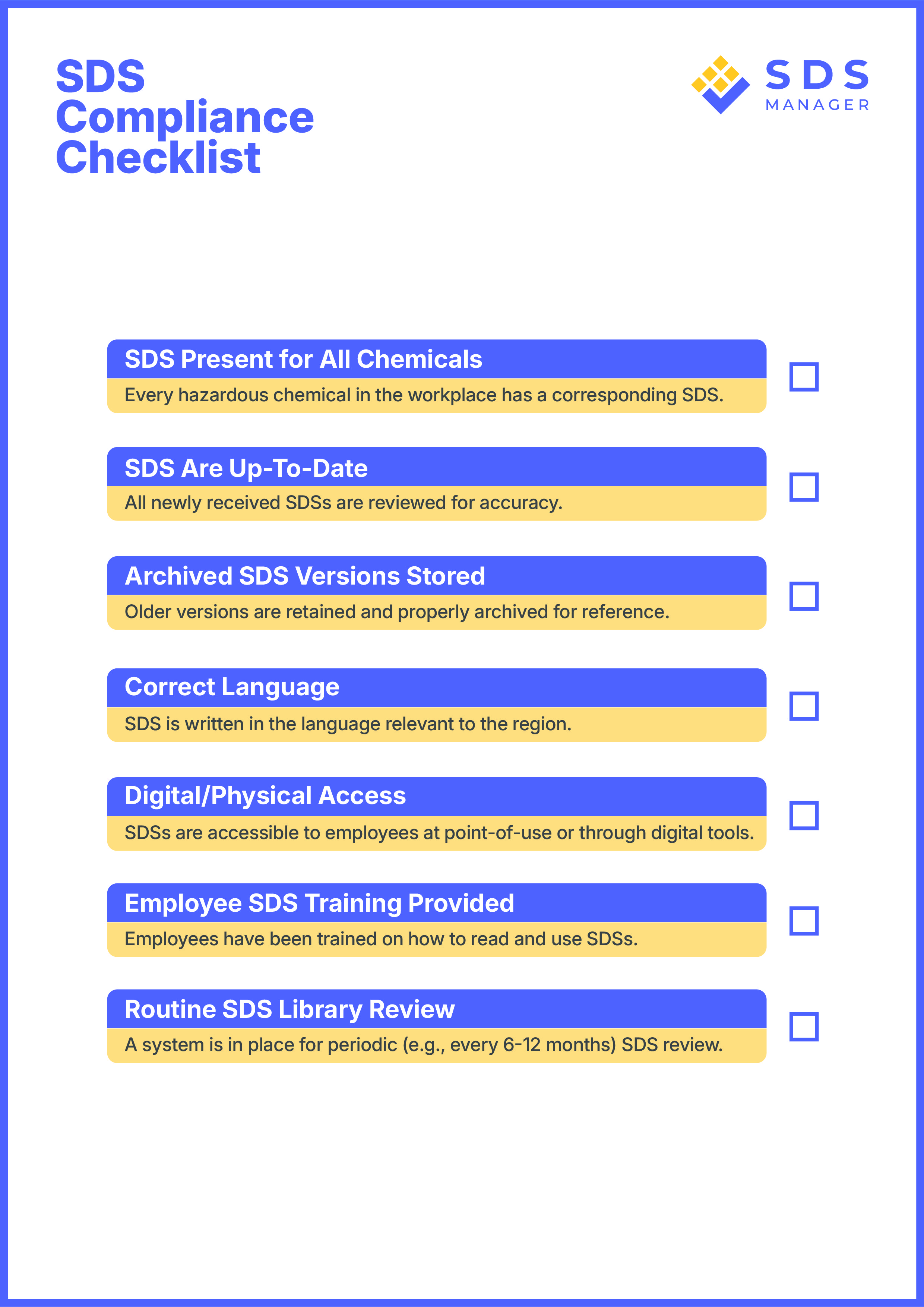
Compliance Is Culture
SDS compliance isn’t just about meeting legal requirements, it’s about creating a safer, more reliable workplace where employees feel valued and protected. Keeping your safety data sheets accurate, up to date, and easy to access helps teams respond quickly to spills, choose the right protective gear, and make smart decisions during emergencies. When everyone understands how to use these documents, safety becomes a shared responsibility, not just a management task. A well-managed SDS system shows your commitment to health, safety, and a culture of care.
How SDS Manager Can Help
SDS Manager is designed to help safety managers stay on top of their SDS responsibilities with tools that align closely with the checklist above.
- Multilingual Access & QR Codes: Provide SDSs in multiple languages with instant mobile access via QR codes.
- Automated SDS Updates: Always stay compliant with the latest SDS versions, automatically sourced from manufacturers.
- One click access to safety information: Safety information is instantly accessible, with hazard details, PPE icons, first aid information, precaution against accidental spills and more. Additionally, a Safety Information Summary can be generated to give employees the essential guidance they need when handling chemicals.
- Generate Secondary container labels: Generate secondary container labels in 15 sizes. Labels feature QR codes, crucial H- and P-codes, and PPE icons.
Getting Started Is Easy
Whether you're building your SDS library from scratch or upgrading your current system for better compliance in 2025, SDS Manager makes the process simple and stress-free. Here's how you can take the next step toward streamlined chemical safety:
- Contact Us For Free Setup Support
- Uncover Features Designed With Your Challenges In Mind
- Book A 1:1 Consultation To Discuss Unique Compliance Needs
Take the First Step Toward Smarter SDS Management: Start Your Free Trial Today!