Create Job Hazard Analysis Reports
Create Job Hazard Analysis Reports (referred to as COSHH Reports in the UK). Read receipts from assigned employees.
See example of Job Hazard Analysis report created using SDS Manager.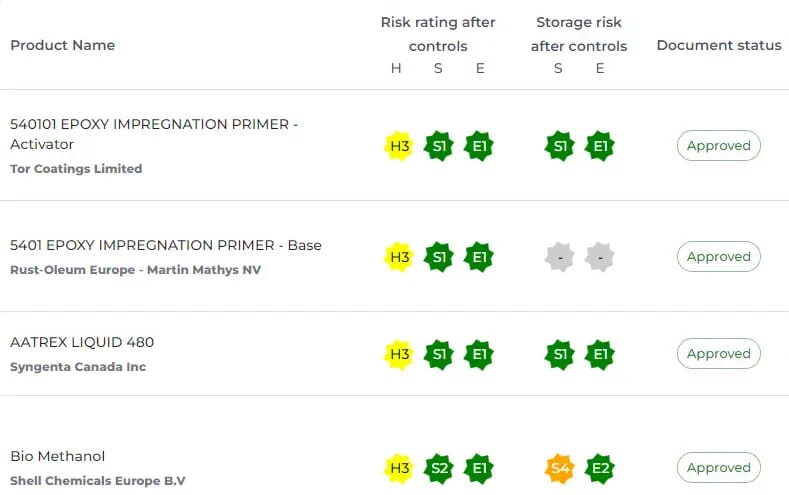
Hazardous products
Use our automated pre-rating of SDS hazardousness to identify hazardous products in your SDS library.
Create Risk Assessment
Create Risk assessment for your Hazardous products
Chemical instruction
The risk assessment can double as a chemical instruction to keep your employees informed about risks and required procedures.
How Job Hazard Analysis works
In SDS Manager, you can create Job Hazard Analysis (Job procedure) according to OSHA REACH and COSHH.
A Job Hazard Analysis is typically used to describe a work procedure involving chemicals, but it is also possible to create work procedures that do not include any chemicals and only use non-substance-related hazards, e.g. Electrical hazards.
Employees can be assigned to the Job Hazard Analysis and can be asked to electronically confirm that they have read and understood the assigned Job Hazard Analysis.
How to create a Chemical Risk Assessment using SDS Manager
The Job Hazard Analysis can be linked to one or more risk-assessed chemicals (SDSs).
Only risk assessed SDS can be linked to the Job procedure.
I.e. you are creating a Job Hazard Analysis involving e.g. 2 chemicals, you first create Chemical risk assessment for each of the two SDSs and then link the risk assessed chemicals to the Job Hazard Analysis.
On the Job procedure risk assessment, the risks will be listed for use without PPE and Controls and the risk with Controls.
SDS Manager use a risk classification range from 1-5 for (H)ealth, (S)afety and (E)nvironment where 3 is the highest acceptable risk for employees
Other features you might like
Chemical risk assessments
Generate Chemical Instruction & Risk Assessment to efficiently educate employees on risks and PPE requirements
Compare products
Side-by-side SDS comparison of two products, allowing for thorough analysis of properties and hazards.
Restricted Substance Notifications
SDS Manager scrutinizes the ingredient details of your chemicals on SDSs and compares them against restricted substance lists.
Free text search
SDS Manager's free text search feature indexes the entirety of the content within all the Safety Data Sheets in your SDS library.