Create Chemical Risk Assessment for hazardous products
Generate Chemical Instruction & Risk Assessment to efficiently educate employees on risks and PPE requirements
See example of Chemical Risk Assessment created using SDS Manager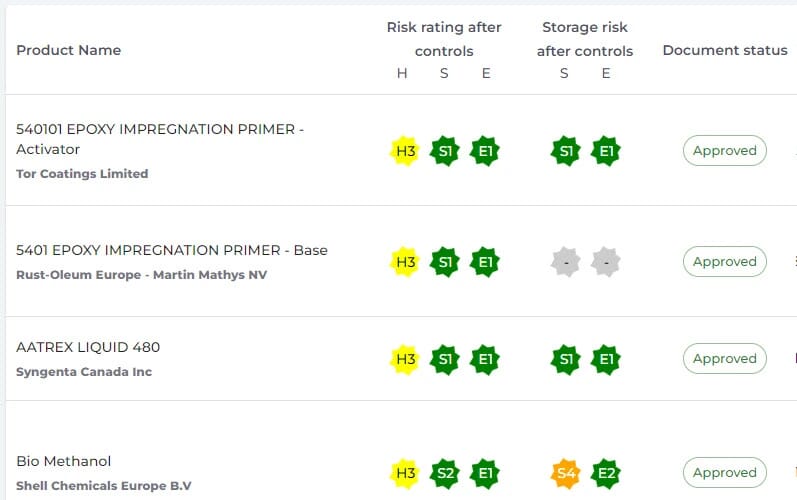
Hazardous products
Use our automated pre-rating of SDS hazardousness to identify hazardous products in your SDS library.
Create Risk Assessment
Create Risk assessment for your Hazardous products
Chemical instruction
The risk assessment can double as a chemical instruction to keep your employees informed about risks and required procedures.
How Chemical Risk Assessment works
Utilize the Risk Assessment module in SDS Manager to generate a comprehensive Chemical Instruction & Risk Assessment document for the chemicals your organization uses. This module also supports the creation of Job Hazard Analysis Reports (referred to as COSHH Reports in the UK), which cater to jobs involving multiple chemicals or other hazards like falls or electrical risks.
Our Risk Assessment process meticulously informs employees about the potential risks associated with handling specific chemicals, while also detailing the necessary Personal Protective Equipment (PPE) and control measures required for safe usage. This ensures a well-informed and protected working environment.
Risk assessments also serve as a tool for documenting adherence to regulations related to the handling and storage of chemicals. They provide a structured approach to ensure compliance, making them essential for maintaining safety standards.
How to create a Chemical Risk Assessment using SDS Manager
Ratings are assigned on a scale from 1 to 5, offering a clear overview of potential risks.
For easy navigation, simply click on the column header to organize your Safety Data Sheets in descending order based on their health hazard rating.
Safety Data sheets that have ingredients on restricted chemical lists are also candidates for products that need risk assessments created.
-
The form of the substance
-
What is the substance used for
-
How the substance should be used
-
How should the substance be disposed of
-
Duration of exposure to the substance when handled
-
Amount of the substance in use when handled
-
Hazard types relevant for handling the substance
-
Classification of risk, classification of exposure and effect of PPE and controls for each hazard type
-
Storage risk regarding safety events
-
Storage risk regarding environmental release events
SDS Manager uses information from the Safety Data Sheet and automatically uses it this in the Risk evaluation.
Based on the H-statements and P-statements in the Safety Data Sheet, SDS Manager will automatically suggest the types of hazards that should be evaluated.
For each of the Hazard types you evaluate the substance risk
E.g. for Skin-hazard, you evaluate how dangerous it is to get the substance in contact with the skin. In this example, we set that to “3-Hazardous” on a 1 to 5 scale.
Next, we evaluate the likelihood that a user of the chemical will come into contact with the skin if no precautions are taken. In this example, we set that to "3- Medium likely"
Assess the impact of PPE and controls on reducing exposure risks.
In this example, we set the effect of the controls to "4-High" resulting in an overall Health-hazardousness score of H3 which is an acceptable risk level. Levels 1 to 3 are regarded as acceptable levels, while levels 4 and 5 are prohibited levels in the workplace.
Upon completing the risk assessments, they can be finalized and approved.
A new revision of the risk assessment can be created when updates are needed.
Other features you might like
Job Hazard analysis
Create Job Hazard Analysis Reports (referred to as COSHH Reports in the UK). Read receipts from assigned employees.
Compare products
Side-by-side SDS comparison of two products, allowing for thorough analysis of properties and hazards.
Restricted Substance Notifications
SDS Manager scrutinizes the ingredient details of your chemicals on SDSs and compares them against restricted substance lists.
Free text search
SDS Manager's free text search feature indexes the entirety of the content within all the Safety Data Sheets in your SDS library.