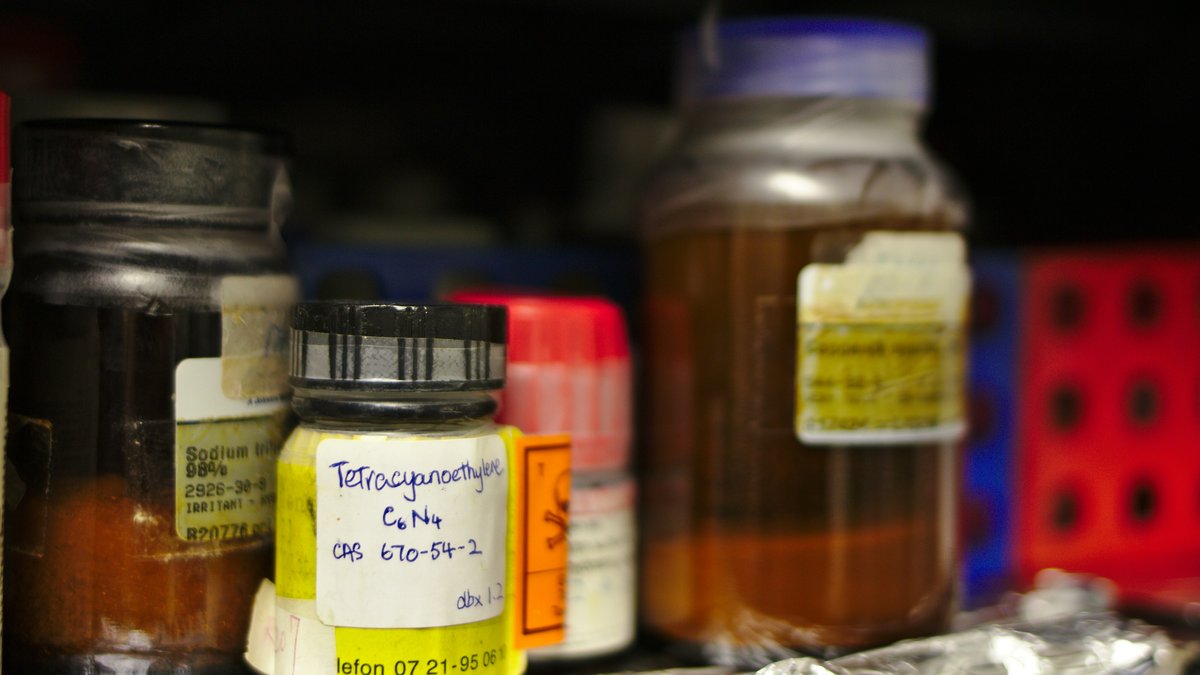
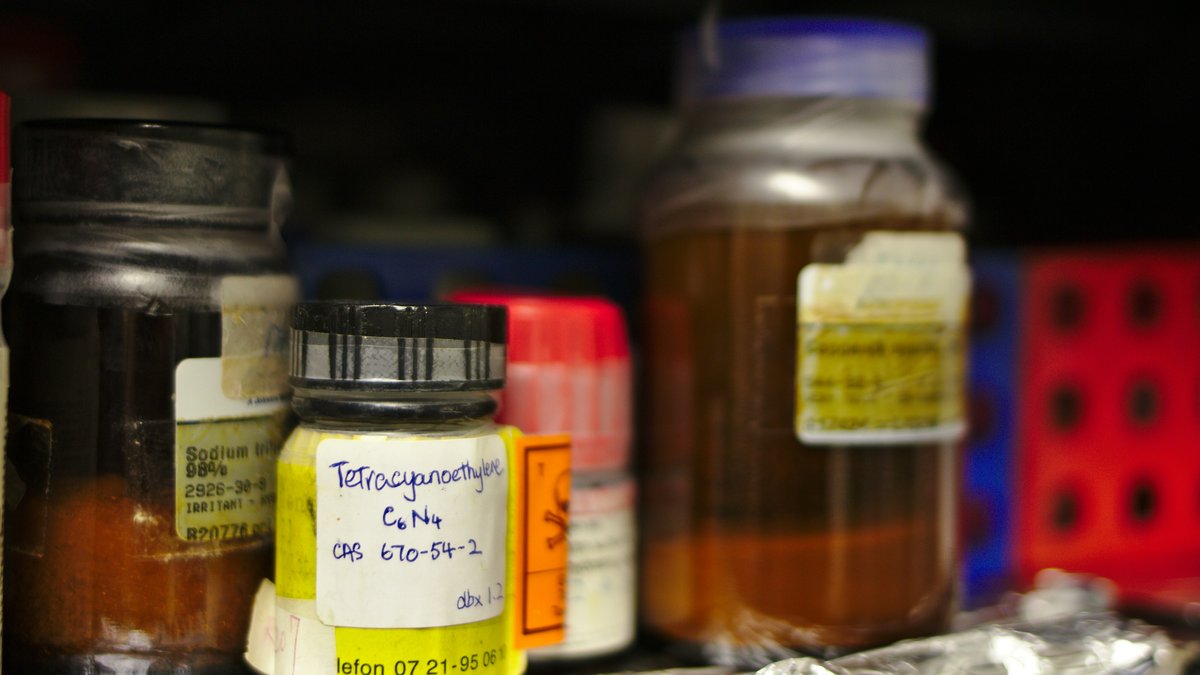
Managing Safety Data Sheets (SDSs) is a fundamental part of chemical safety in the workplace. Every organization that uses chemicals, like in manufacturing, labs, construction, or office work, must collect and store SDSs. They should also make these documents easy for employees to access.
Many businesses have trouble managing SDS. They may not know how to begin or use old methods that make compliance hard. This guide will take you through the entire SDS management process, breaking it down into six clear steps.
What is SDS Management?
SDS management involves organizing, storing, and tracking your Safety Data Sheets for every chemical in your business. It ensures that employees can easily access these sheets when needed. The information must be correct. It should also follow rules like OSHA (Occupational Safety and Health Administration) and GHS (Globally Harmonized System).
Step-by-Step Guide to SDS Management
Step 1: Creating an Overview of Chemicals
The first and most crucial step is identifying all the chemicals used in your workplace. Many companies lack clear records of the chemicals they use. This can lead to missing SDSs, improper handling, and regulatory issues. Without an overview, managing and collecting SDSs and ensuring safety measures becomes impossible.
To get started, list every chemical present in your facility. Check all areas where chemicals are stored, used, or disposed of. This includes storage rooms, laboratories, maintenance areas, and production floors. Walk through each section systematically and document every chemical container you find. For each chemical, record key details such as its name, manufacturer, and storage location. Keeping an organized list of chemicals will set you up for an effective SDS management system.
Step 2: Finding and Collecting SDSs
Once you have a complete list of chemicals, the next step is to gather the corresponding Safety Data Sheets. This is where many businesses face challenges because SDSs are not always easy to find. Some companies still use paper binders from suppliers. Others may have trouble finding SDSs for older or rare products.
Here are several ways to search for SDSs effectively:
- Search online: Manufacturers and suppliers usually post SDSs on their websites. A quick Google search with the right terms can help you find them. Try searching terms like "Safety Data Sheet [Product Name]" or "[Product Name] SDS PDF" to get accurate results.
- Use SDS databases: Another good choice is to use SDS databases. These platforms give access to thousands of SDSs. Businesses can search and download the latest versions quickly. This method is much more efficient than searching online by hand. It removes the guesswork in checking if SDSs are valid. SDS Manager offers a free SDS database where businesses can easily search for and find up-to-date SDSs for chemicals.
- Reach out to suppliers: If you cannot find SDSs for chemicals online, you may need to contact suppliers directly. You can request the latest version of the SDS for each chemical purchased via email or phone.
To gather SDSs for all your chemicals, you can effectively use a mix of Google searches, SDS databases, and direct communication with suppliers.
Step 3: Organizing Your SDS Library
Having SDSs is not enough—they must be organized so employees can easily find them when needed. Here are three ways you can organize your SDS library.
Creating a Paper Binder System:
Traditionally, businesses have used paper binders to store printed SDSs in a central location. If you prefer paper binders, categorize printed SDSs by logical labels and store them in dedicated binders. Keep the binders organized so each SDS is easy to retrieve. Here’s how to create a paper binder system:
- Categorize Your Chemicals: Group your chemicals based on logical categories. Examples include:
- Alphabetical order by chemical name.
- Alphabetical order by manufacturer.
- Location of use or storage.
- Allocate Binders: To keep your Safety Data Sheets (SDSs) organized and easy to access, it’s a good idea to plan how many binders you’ll need based on the total number of SDSs and how you want to categorize them. As a general rule of thumb, try to keep each binder to around 25–50 SDSs. This makes the binder easier to handle and ensures that employees can quickly flip through the pages when needed. Keeping binders lightweight also makes it simpler to update or replace SDSs when changes happen. If you’re managing a large number of SDSs, using multiple binders will help keep things neat, accessible, and OSHA-compliant.
- Print and Insert SDSs: Print a hard copy of each SDS and insert it into the appropriate binder. Using sheet protectors for your SDSs isn’t mandatory, but it’s definitely a good practice. They help prevent wear and tear from frequent handling, protect against spills or smudges. If you want to keep your SDSs in good condition over time—especially in high-use areas—adding sheet protectors is a simple way to do that.
- Create an Index:
- For each binder, create a detailed index at the front.
- Include the chemical name and page number (if you number the pages within the binder).
- Consider a master index if you have numerous binders, listing the binder and the chemicals found within.
- Consider keeping a digital version (e-binder) of the paper binder. Here’s a good example of one.
- Strategic Placement of Paper Binders: Instead of a single central location, store SDS binders in multiple readily accessible locations wherever chemicals are stored or used within your facility. Ensure all employees know the location of the SDS binder(s) relevant to their work area.
Drawbacks of Paper Binders:
While this method is simple, it has major challenges. SDS paper binders can quickly become outdated, and searching through them during an emergency can waste valuable time. Maintaining a physical index also requires constant updates, which can be tedious and prone to errors.
Creating a Folder-Based System:
A more modern approach is to create folder based system by organizing SDS PDFs into clearly labelled folders or subfolders based on location name & structure. Store these folders on cloud storage so your team can access them when they need it.
To create a folder based system, decide on a clear and logical folder structure on your shared cloud storage or network drive. To keep your digital SDS library organized and easy to navigate, start with a main folder named after your company. Inside this folder, create subfolders for each site or facility (e.g., "Headquarters," "Plant B"). Within each site folder, you can create additional layers based on departments, buildings, specific areas, or even floors. This hierarchical setup helps you quickly locate the SDS you need without digging through unrelated files and keeps your chemical documentation neatly separated. For a visual guide, you can check out the flowchart below to help you visualize a folder structure.
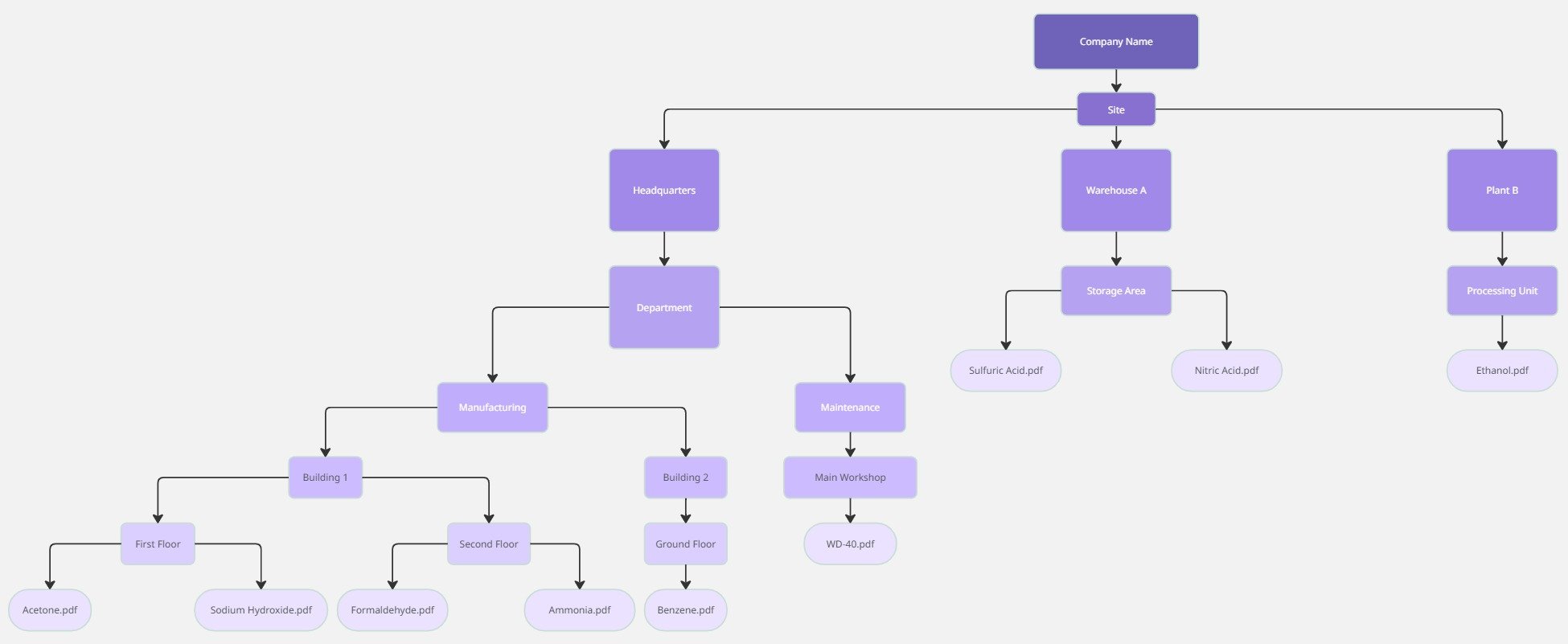
Drawbacks of a Folder-Based System:
This method is better than paper binders because employees can get SDSs from any location. However, it still has some drawbacks. Folder storage requires manual organization and indexing. As the number of SDSs grows, keeping everything properly categorised becomes harder and more time-consuming. Maintaining links and ensuring everyone follows the naming conventions can also be challenging.
Using an SDS Management System:
The most efficient solution is to use SDS management software. This software automatically organizes SDSs, making them easy to search by chemical name, manufacturer, CAS no, SAP/ERP ID. Features like bulk import, filtering, generating secondary container labels, chemical risk assesment and EPA reporting can help you organise your SDS library effortlessly. All of which are features of our SDS management tool. Using an SDS management system eliminates many of the drawbacks associated with both paper and basic e-binder systems, ensuring your SDS library is always up-to-date and organized.
Step 4: Making SDSs Easy to Access
Even with a well-organized SDS library, accessibility remains a key concern. In many workplaces, employees struggle to locate SDSs when they need them the most—especially in emergencies. A slow response time can put workers at risk and lead to regulatory penalties.
To solve this, companies should implement multiple access points for SDS retrieval. If you're using paper binder SDSs, place binders in easily accessible locations like break rooms, workstations, and chemical storage areas.
However, a more effective approach is to use SDS management software with digital access tools like QR codes and barcode scanning, which are features of our SDS management tool. Place the QR code posters in areas where it is easy for employees to access when needed the most, such as areas where chemicals are regularly handled. With mobile apps, QR codes, and barcodes, businesses can make SDSs easily accessible whenever and wherever safety information is needed.
Step 5: Keeping SDSs Up to Date
A significant challenge in SDS management is maintaining current and accurate safety information. Regulatory requirements mandate regular review and updates as chemical formulations and safety guidelines evolve.
The best practice is to review your SDS library at least every two years, replacing older versions with the latest ones obtained through online searches, supplier contact, or automated tracking systems. For paper-based systems, this means setting a regular review schedule, immediately replacing outdated SDSs, and updating the index accordingly. Similarly, for digital folder-based systems, it's important to routinely check and replace outdated PDF files while ensuring new chemical SDSs are added correctly.
To simplify this process, SDS Manager offers powerful tools that reduce the burden of manual tracking. Our system automatically monitors thousands of supplier websites and notifies you when a new SDS version becomes available. You can also choose to receive email notifications about updates directly from our free SDS Search Page. Here’s how to use the free SDS search tool:
- Go to our free SDS search page.
- Use the search bar to enter a chemical name, product, supplier, CAS number, UFI number, or EU number.
- Our tool will scan our database of over 13 million SDSs and display relevant results.
- From there, you can download and print the SDS you need.
- Click the email notification option on the SDS page to be notified whenever an updated version becomes available.
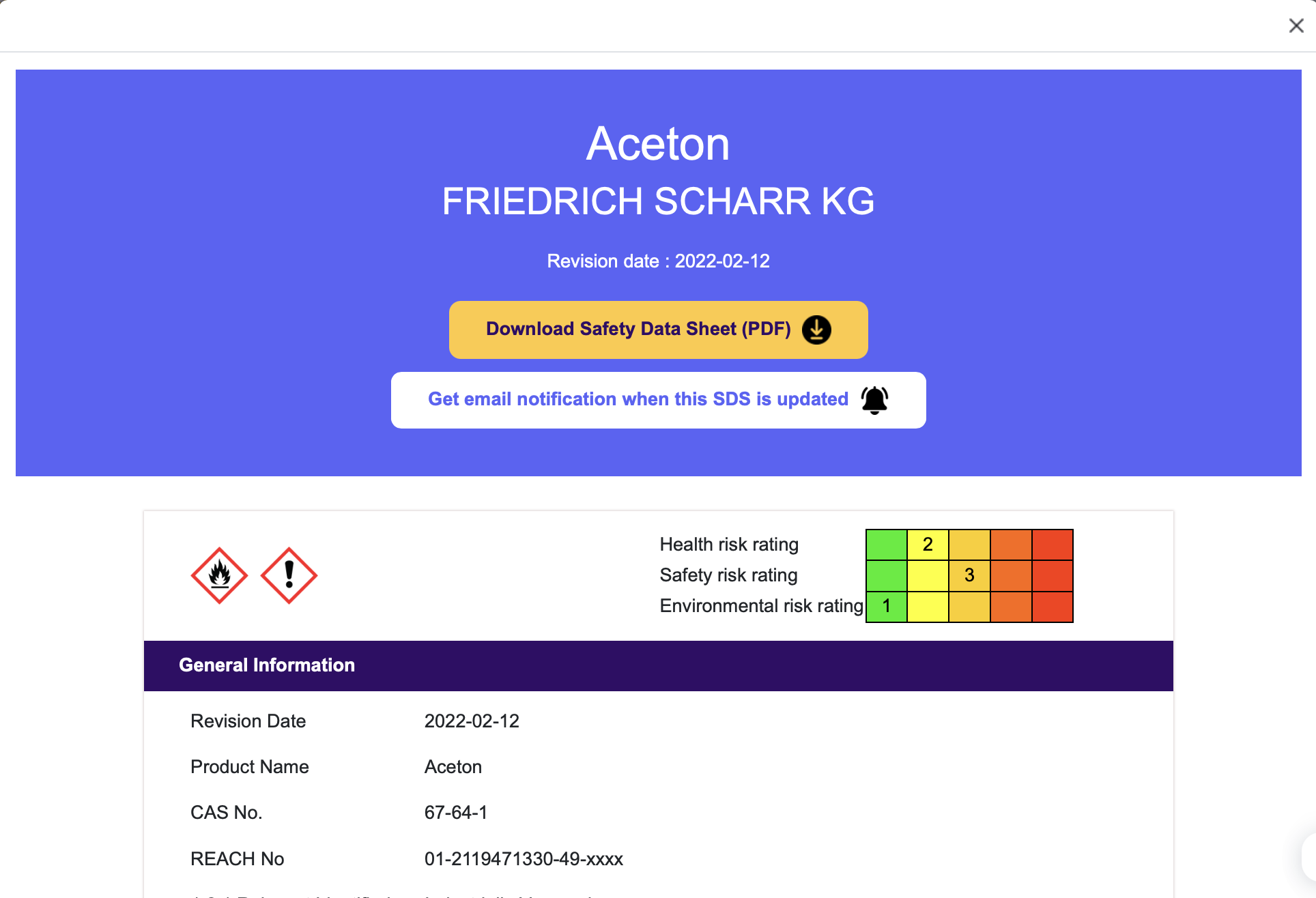
Step 6: Training Employees on SDS Use
Even with a perfect SDS management system in place, it is useless if employees don’t know how to use it. Many workers are unfamiliar with how to read an SDS, what information to look for, or where to find SDSs in an emergency. To ensure employees can effectively use SDS, training should include a comprehensive, hands-on approach with real-world scenarios. Key training methods include:
- Understanding SDS Structure: SDS typically consists of 16 sections, covering chemical identity, hazards, first-aid measures, and more. Employees should be trained to quickly identify and understand these sections so they can respond effectively in emergencies.
- Hands-On Training: Practical workshops, role-playing, and simulation exercises help employees interact with SDS documents and practice applying their knowledge in real-life scenarios, like chemical spills.
- Integration with Safety Programs: SDS training should be included in broader safety programs. It should start during employee orientation and continue with regular refresher courses to keep workers updated on new chemicals or regulatory changes.
- Continuous Learning and Updates: Given the evolving nature of chemical safety regulations, companies should commit to continuous learning. Regular workshops and access to updated SDS databases are key to keeping employees informed about the latest regulations and safety measures.
- Promoting Open Communication: Foster a culture of safety where employees feel comfortable asking questions about SDS and safety practices. Hold regular safety meetings and open forums to keep employees engaged and allow them to address any concerns about chemical handling and safety protocols.
By using a multi-faceted training approach, employees can learn how to handle hazardous chemicals safely. This reduces risks and improves safety compliance.
How Can SDS Manager Help?
To easily manage your Safety Data Sheets (SDSs) library and ensure you're always prepared, consider how SDS Manager can streamline your processes. Our tool is designed to make SDS management easier, allowing you to focus on running your business while staying safe and compliant. Learn how to get started with SDS Manager to easily manage your Safety Data Sheets (SDSs) library.
Here’s how we can help:
- Free Setup & Training: We source your SDS and set up your online SDS library for free.
- QR Code access: Instant SDS access for employees through intranet links, QR code posters or SDS app for IOS/Android
- Stay Up to Date: We automatically keep your safety data sheets up to date.
- Generating NFPA Labels: Easily boost workplace safety with SDS Manager’s automated NFPA label generator—instantly create and customize labels that clearly show accurate hazard information.
- And More: From advanced search tools to employee SDS request features—we’ve built everything you need to stay compliant and organized.
Managing SDSs is a key step in maintaining a safe and compliant workplace. By properly collecting, organizing, and keeping your SDSs up to date, you empower your team to respond confidently in emergencies. Make sure to provide regular training and stay proactive with compliance.
Book a 1:1 call with us to get a personalized demo or discuss how SDS Manager can help streamline your SDS management!