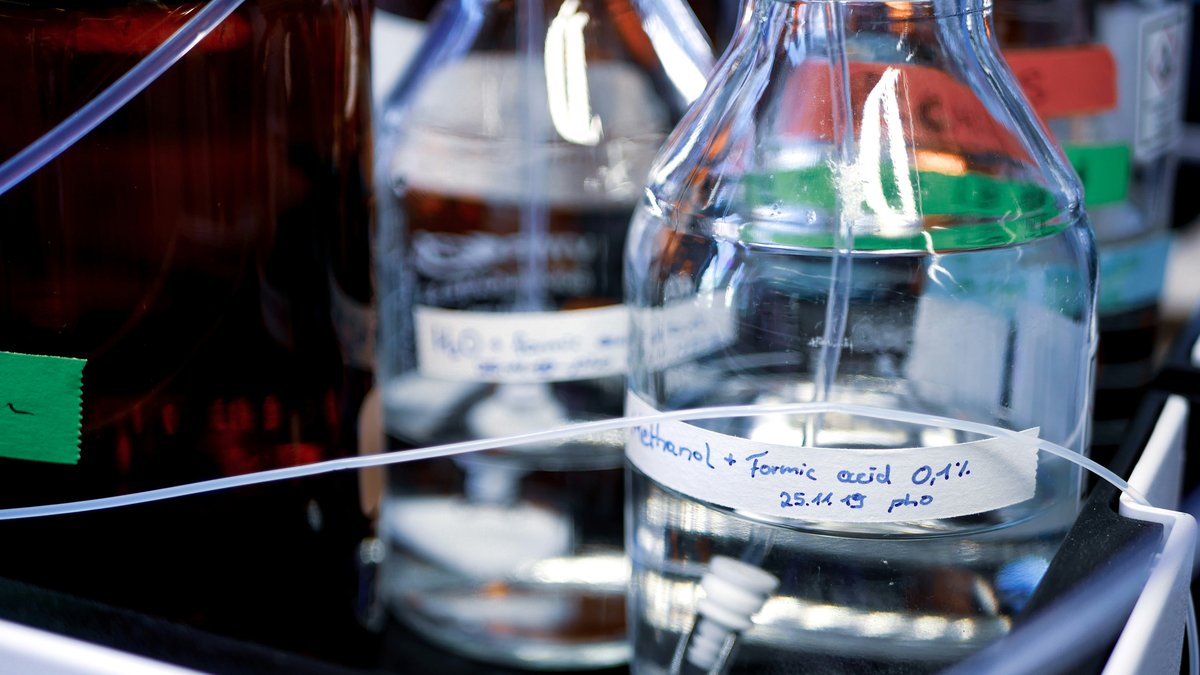
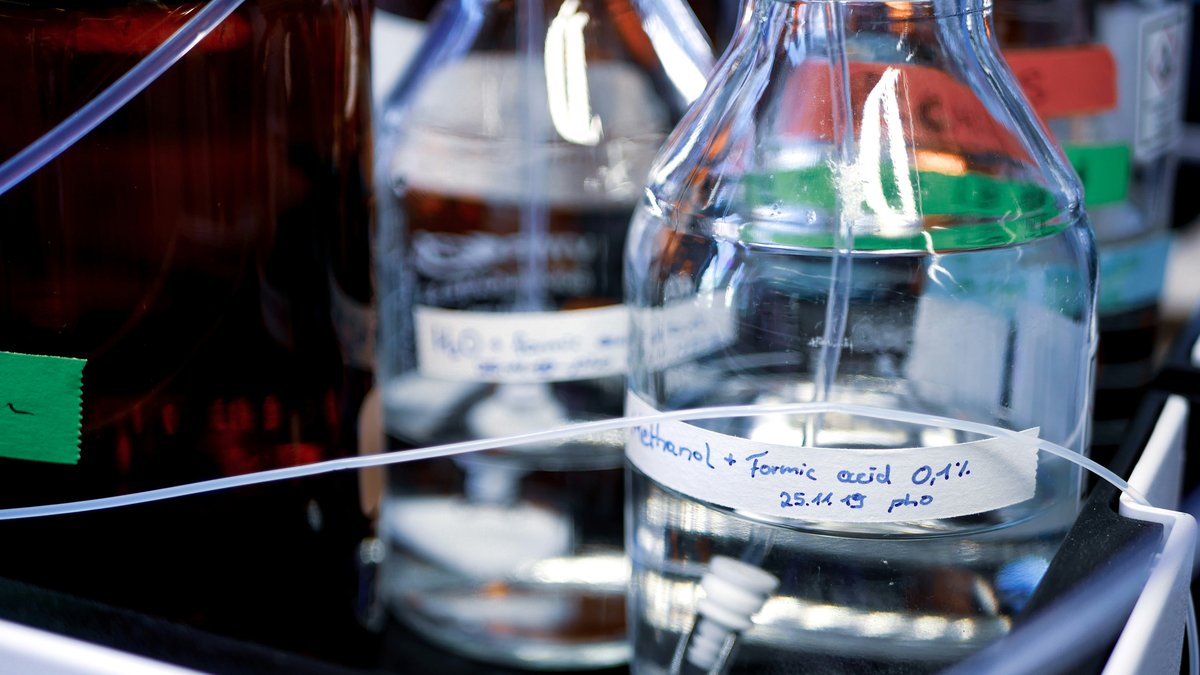
The European Union (EU) is implementing important updates to its Classification, Labelling, and Packaging (CLP) Regulation. These changes introduce new CLP hazard classes that chemical manufacturers, distributors, and chemical managers must understand thoroughly. These updates will have significant implications for safety data sheet (SDS) compliance, workplace safety through enhanced hazard communication, and overall product compliance within the EU market.
Key Changes to the CLP Regulation
The CLP Regulation, which is designed to align with the Globally Harmonized System (GHS) for classifying and labeling chemicals, is being strengthened with the addition of new hazard classifications. These new classes reflect a growing scientific understanding of the potential risks chemicals pose to both human health and the environment. The latest regulatory updates include the following significant hazard categories:
- Endocrine Disruptors (EDs): New, specific classifications are being introduced for substances identified as endocrine disruptors. These are chemicals that can interfere with the body's hormonal system, potentially leading to a range of adverse health effects. The new classifications will categorize endocrine disruptors based on the target of their disruptive effects:
- ED for human health (Category 1 & 2)
- ED for the environment (Category 1 & 2)
- Persistent, Bioaccumulative, and Toxic (PBT) / Very Persistent and Very Bioaccumulative (vPvB) Substances: The criteria for identifying substances that are PBT or vPvB are being expanded and clarified. These substances pose long-term environmental risks due to their ability to persist in the environment, accumulate in living organisms, and exhibit toxic effects.
- Persistent, Mobile, and Toxic (PMT) / Very Persistent and Very Mobile (vPvM) Substances: This is a newly established classification for chemicals that possess a combination of concerning properties. PMT/vPvM substances are characterized by their persistence in the environment, their high mobility (allowing them to easily migrate through soil and water), and their inherent toxicity. This new category specifically addresses the potential for these chemicals to contaminate water sources and pose widespread environmental risks.
Impacted Stakeholders
The following changes to the CLP Regulation will affect a broad spectrum of stakeholders involved in the chemical supply chain:
- Chemical Manufacturers: These companies will bear the primary responsibility for re-evaluating the hazard profiles of their chemical products based on the new CLP Hazard Classes. This will necessitate updating their internal classification processes and subsequently revising their safety data sheets (SDS) to accurately reflect the new hazard information.
- Suppliers and Distributors: Businesses involved in the supply and distribution of chemicals will need to ensure that the labels and packaging of the products they handle are compliant with the new hazard classifications and display the updated hazard information. This is crucial for effective hazard communication throughout the supply chain.
- Workplace Safety Officers and SDS Managers: Individuals and teams responsible for workplace safety will need to ensure that updated safety data sheets (SDS) are readily available to all workers who handle these chemicals. Furthermore, they will be responsible for implementing appropriate hazard communication training programs to ensure that workers understand the new hazard categories and the associated risks, contributing to overall chemical safety in the workplace.
Compliance Timelines
To allow stakeholders sufficient time to adapt to these changes, the EU has established specific compliance deadlines that depend on whether the substance or mixture is new or already on the market:
- Substances newly placed on the market: The new classification rules apply from May 1, 2025.
- Existing substances on the market: The deadline to comply with the new classification is November 1, 2026.
- Mixtures newly placed on the market: The new classification rules apply from May 1, 2026.
- Existing mixtures on the market: The deadline to comply with the new classification is May 1, 2028.
Preparing for the New CLP Hazard Classes: A Proactive Approach
The new CLP hazard classes were introduced via Commission Delegated Regulation (EU) 2023/707, which entered into force on May 1, 2023. To ensure a smooth transition and maintain SDS compliance and chemical safety, chemical managers and other affected stakeholders should adopt a proactive approach:
- Thorough Chemical Inventory Review: Conduct a comprehensive review of your current chemical inventory to identify any substances that may now fall under the scope of the new CLP hazard classes, particularly those with potential endocrine disruptors, PBT/vPvB, or PMT/vPvM properties.
- SDS and Label Updates: Take immediate steps to update your safety data sheets (SDS) and product labels to ensure full compliance with the new classification requirements for all affected substances. Accurate and up-to-date SDS compliance is paramount.
- Comprehensive Employee Training: Develop and implement thorough training programs for all employees who handle chemicals. These programs must cover the details of the new CLP hazard classes, the associated potential health and environmental risks, and the necessary safe handling procedures, reinforcing effective hazard communication and workplace safety.
- Continuous Monitoring of Regulatory Updates: Stay diligently informed about the latest regulatory updates issued by EU regulatory bodies regarding the CLP Regulation. This includes monitoring official publications for specific deadlines, additional guidance documents, and any further amendments or clarifications.
The introduction of these new CLP hazard classes represents a significant advancement in chemical safety regulations within the European Union. Chemical managers and chemical manufacturers must take proactive and timely steps to ensure full SDS compliance, update their hazard communication practices, and adequately educate their teams on these crucial changes. Failure to comply with these evolving regulations can lead to significant regulatory penalties and increased liability risks. For organizations navigating these complex regulatory updates, investing in a robust SDS compliance management system can significantly streamline the process of updating safety documentation and ensuring ongoing adherence to the latest requirements, ultimately contributing to enhanced workplace safety and a reduction in potential environmental risks.