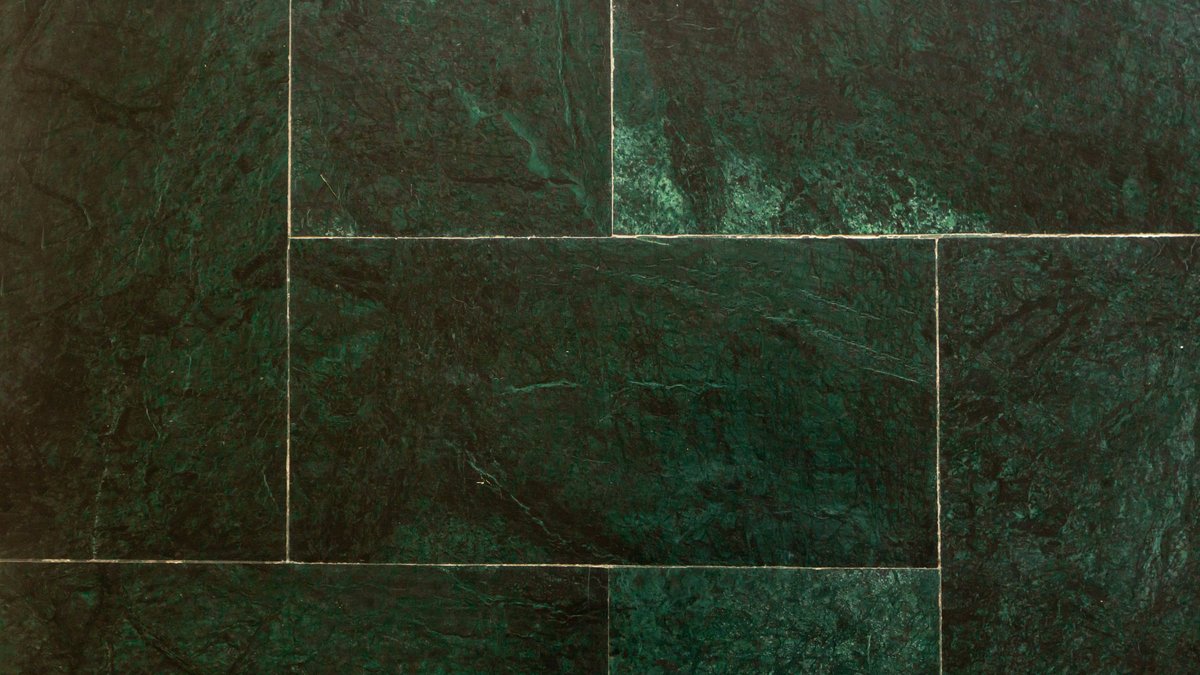
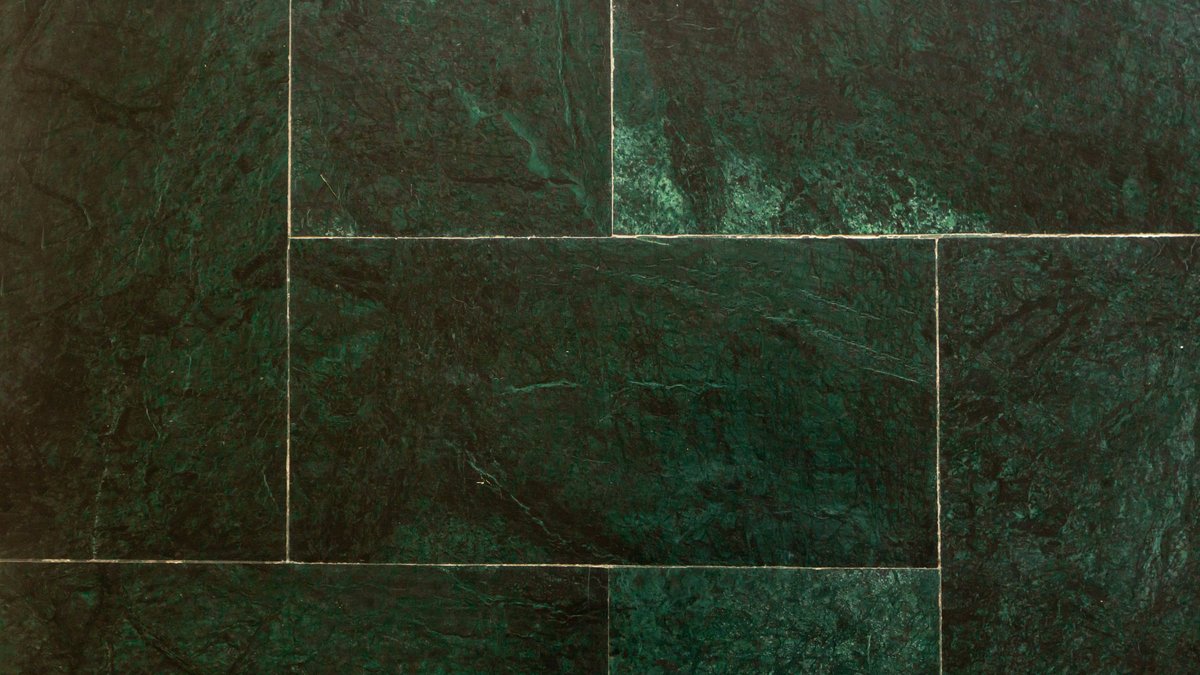
Safe Work Australia is seeking detailed feedback on how well the Engineered stone ban is working. This ban started on July 1, 2024, across Australia. It was a strong step to improve worker safety regulations by greatly reducing or completely stopping workers from being exposed to respirable Crystalline silica. This dangerous substance comes from making and working with engineered stone. Studies have linked it to serious and sometimes deadly lung diseases, especially Silicosis prevention. The ban is a very important part of Australia's promise to protect workers' health in building, manufacturing, and related jobs.
Public Consultation on the Engineered Stone Ban
Gathering Feedback for Regulatory Improvement
Safe Work Australia is carefully collecting detailed information and real-world experiences about how the engineered stone ban is being used. This is part of their regular review. They want to understand several things: how state and territory organizations are enforcing the ban, if businesses (especially smaller ones) have the safety resources and support they need to follow the rules, and if the current rules are strong enough or if they need changes to achieve crystalline silica safety better.
Encouraging Stakeholder Participation
Because of this, employers, workers affected by the ban, industry groups, health and safety experts, and other important people are highly encouraged to take part in this important public consultation on safety. They should openly and honestly share what they've experienced, what they've seen, any problems they've faced, and any ideas they have for making things better. This helpful feedback will be key in deciding the future path of worker safety regulations and the specific steps taken to protect Australian workers from the dangers of respirable crystalline silica.
Consultation Timeline and Submission Process
The public consultation on safety is open now and will close on March 31, 2025. This gives everyone who wants to share their views plenty of time. You can easily send your responses and submissions through Safe Work Australia’s Consultation Hub, which is an easy-to-use online site to gather and study your feedback. All the information and ideas collected will be carefully looked at and put together to create a detailed official review. This review will then be given to the Work Health and Safety (WHS) ministers from all Australian states and territories so they can think about it, discuss it, and decide if any changes or plans are needed for the engineered stone ban and wider worker safety regulations.
Implications for Safety Data Sheets (SDS) Compliance
Ensuring Accurate Hazard Communication
The current review of the engineered stone ban is important for safety data sheets (SDS) compliance in many industries dealing with hazardous materials. Because respirable crystalline silica is known to be hazardous, businesses that use or handle products with silica, even if the engineered stone ban doesn't directly apply to them, must make sure their safety data sheets (SDS) are current, complete, and follow the WHS regulations in their area.
Key Aspects of SDS Compliance
- Accurate Hazard Classification and Labeling According to Workplace Safety Standards: Businesses need to correctly identify and classify the dangers of the materials they use, including if respirable crystalline silica is present and could cause exposure. This classification must be shown clearly on product labels and containers, giving immediate warnings that are easy for workers and others to understand. These labels must strictly follow the rules in the relevant workplace safety standards and WHS regulations.
- Maintaining updated SDS for Safe Handling of Hazardous Substances: Safety data sheets (SDS) are the main source of information about the dangers, safe handling, emergency steps, and disposal of hazardous substances. Businesses must constantly make sure their safety data sheets (SDS) are reviewed and updated. This includes changes in laws, new scientific information about the substance's dangers, or updates to safe handling practices for hazardous substances management. These documents need to give clear and practical advice to workers on how to work safely with the material, such as using the right personal protective equipment (PPE), ventilation needs, and what to do if there are spills or accidental exposure.
- Providing Proper Training and Hazard Communication for Worker Safety: Just having correct and up-to-date safety data sheets (SDS) isn't enough. Businesses also have to make sure their workers get full and ongoing training on the dangers of the materials they work with, including the specific risks of respirable crystalline silica. This training should cover the information in the safety data sheets (SDS), correct safe work methods, how to properly use and maintain PPE, and emergency procedures. Good hazard communication is a key part of worker safety regulations, making sure workers know the risks and how to protect themselves.
Broader Focus on Hazardous Substances Management
Anticipating Increased Regulatory Scrutiny
The current review of the engineered stone ban shows a wider and stronger focus on effectively regulating hazardous substance management in all Australian industries. Businesses working with silica in any form and those using similar hazardous materials should expect closer checks and more attention to making sure they have strong chemical safety compliance.
Potential Future Regulatory Measures
- More Workplace Inspections to Ensure SDS Documentation and Safety Measures Meet Standards: Regulatory authorities will probably inspect workplaces more often and more thoroughly. This is to check if businesses are following the rules for chemical safety compliance. These checks will focus on making sure that correct and up-to-date safety data sheets (SDS) are easy to find, that proper safety steps are being taken, and that these steps follow the rules of workplace safety standards and WHS regulations.
- Stricter Safety Rules for Crystalline Silica & Limits on Worker Exposure: As we learn more about the long-term health effects of being exposed to dangerous substances like respirable crystalline silica, regulators might set stricter limits on how much workers can be exposed. They might also require stronger protective measures for workers who handle these materials. This could mean needing better respiratory protection, stronger ventilation systems, and tighter controls on how work is done. All of this would further strengthen crystalline silica safety and help with silicosis prevention.
- Greater Focus on Engineering Controls and Safer Material Alternatives: A main idea in good hazardous substances management is to first try to get rid of or replace dangerous materials if possible. Regulatory efforts will likely push harder to encourage and sometimes require the use of engineering controls, like dust collection systems and local exhaust fans. These help reduce how much workers are exposed at the source. Also, there will likely be a continued effort to find and use safer alternative materials that can lower or remove the risks of hazardous substances like crystalline silica.
Proactive Steps for Chemical Safety Compliance
Looking ahead, as Australia keeps working to improve workplace safety standards and make sure there's good chemical safety compliance, it's crucial for businesses to stay up-to-date on all the new rules and change how they work to avoid problems with compliance, fines, and most importantly, to keep their workers healthy and safe. Employers should take immediate and continuous steps to carefully check and, if needed, completely revise how they manage their safety data sheets (SDS). This will ensure that all safety information is always current, correct, easy for everyone to find, and fully follows the newest WHS regulations and workplace safety standards.
For people and businesses who want more detailed and current information about the engineered stone ban, what's needed for chemical safety compliance, and the best ways to handle hazardous substances management, the Safe Work Australia website is the best place to go. Also, businesses are strongly advised to talk directly to the WHS regulations authority in their state or territory for specific advice and help that fits their situation and the local rules. By making worker safety regulations a priority and actively working towards chemical safety compliance, Australian businesses can help create healthier and safer workplaces for everyone in the country.