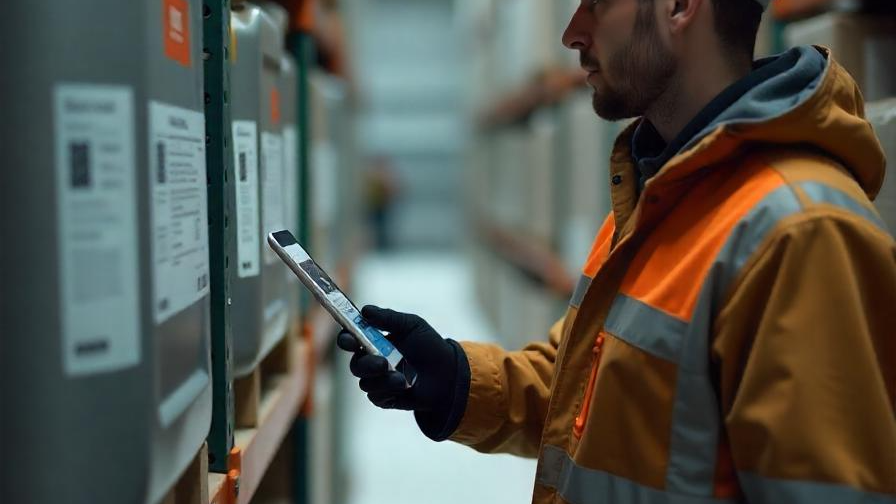
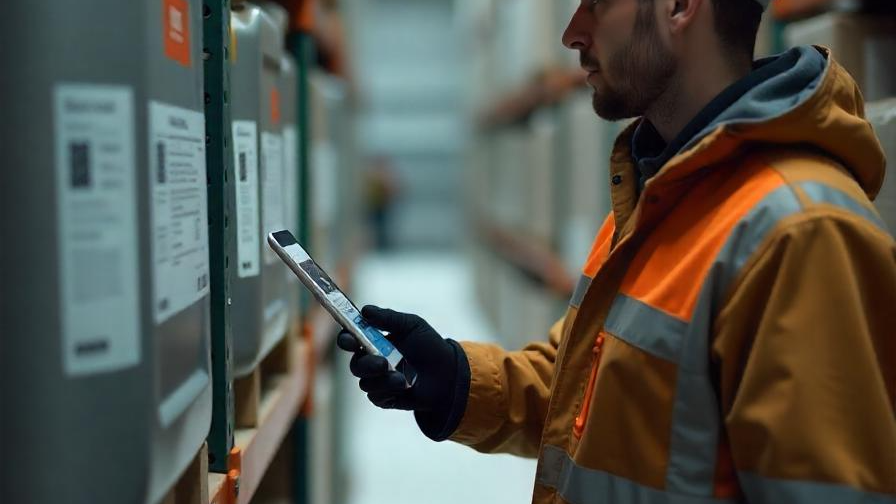
What is SDS Management?
SDS management is all about organizing, storing, tracking, and keeping your Safety Data Sheets up-to-date for every chemical used in your business. It’s making sure that employees can easily access these sheets when they need them and that the information is always accurate and compliant with regulations like OSHA (Occupational Safety and Health Administration) and GHS (Globally Harmonized System).
Step-by-Step Guide to SDS Management
Step 1: Collect All SDSs
The first step is gathering all the SDSs for the chemicals your company uses. Whenever you buy a new chemical, you should get the SDS from the manufacturer or supplier. Always make sure the SDS is current and accurate.
Tip: Don’t forget to ask for an updated SDS from your supplier every time a new version is released.
Step 2: Organize Your SDS Library
Once you’ve collected your SDSs, the next step is to organize them so they’re easy to find. You can choose between a physical system or digital system for storing your SDSs.
- Digital System – A cloud-based system is the most efficient way to store SDSs. It allows you to quickly search and access SDSs from anywhere.
- Physical Storage – If you prefer physical storage, use a well-organized binder or file system to keep SDSs in order.
Tip: Label your SDSs clearly and consistently (by chemical name or product code) to make finding them easier.
Step 3: Make SDSs Easy to Access
Your employees need quick access to SDSs, especially in case of an emergency. You can give them access in a few different ways:
- Digital Access: Set up intranet links or use a mobile app for easy access.
- Physical Access: Keep physical copies of SDSs in accessible locations, like near workstations where chemicals are used.
Tip: QR codes can be a great way to give employees instant access to SDSs via their smartphones.
Step 4: Keep SDSs Up-to-Date
SDSs need to be updated regularly to stay in line with new regulations or if new hazards are discovered. This means reviewing your SDSs at least once a year or whenever there are changes in the law.
- Stay on top of changes in OSHA or GHS regulations to make sure your SDSs reflect the latest rules.
- Replace outdated SDSs with new ones from suppliers as soon as they become available.
Tip: Set up reminders to review and update your SDS library on a regular basis.
Step 5: Train Your Employees
Training your employees on how to read and use SDSs is crucial for safety. They need to understand the information in each section and know what to do in an emergency. Your training should cover:
- SDS Sections: Help employees understand what each section of an SDS means, such as hazard identification, first aid measures, and fire-fighting steps.
- Safety Measures: Teach employees the proper handling, storage, and protective measures for each chemical.
Tip: Offer refresher courses and make training materials available for employees to review.
Step 6: Stay on Top of Compliance
SDS management isn’t a one-time task. You need to stay on top of regulatory changes and make sure your SDSs are always compliant. Regular audits of your SDS library will help ensure everything is up-to-date and in line with safety regulations.
- Audit your SDSs regularly to catch outdated information or missing sheets.
- Track regulatory changes to ensure your SDSs meet the latest standards.
Tip: Use a compliance management tool to help you keep track of updates and regulations.
Step 7: Create a Hazard Communication Program
A good hazard communication program is all about making sure everyone in your company knows how to stay safe when working with chemicals. This program should include clear communication about SDSs, labeling, employee training, and emergency procedures.
Tip: Link your SDS management system with your overall safety program for better results.
Why is SDS Management Important?
Good SDS management does a lot of important things:
- Keeps Workers Safe – SDSs tell workers about the risks of chemicals, how to handle them, and what safety gear to wear.
- Helps Stay Compliant – Following regulations helps avoid fines and ensures your business is up to code.
- Prepares for Emergencies – SDSs give clear instructions for first aid, fire response, and chemical spill cleanup.
Protects the Environment – Proper disposal instructions on SDSs help prevent chemicals from harming nature.
How Can SDS Manager Help?
Managing SDSs manually can be a lot of work, especially when your company handles many chemicals. SDS Manager can make the process much easier with its chemical compliance software.
Here’s how we can help:
- Easy Access: Store all your SDSs in one secure, online location that’s accessible anytime, anywhere.
- Automatic Updates: SDS Manager automatically updates your SDSs, so you don’t have to worry about staying compliant.
- Free Setup and Training: Get your SDS library set up for free, and train your team without the hassle.
- QR Code Access: Use QR codes to give employees instant access to SDSs from their phones.
- Compliance Tracking: Stay on top of regulatory changes with automatic tracking to ensure you’re always in compliance.
- Custom Solutions: SDS Manager can be tailored to fit your business size, industry, and safety needs.
By using SDS Manager, you can simplify SDS management, reduce compliance risks, and improve overall workplace safety.
Conclusion
Managing SDSs is an essential part of keeping your workplace safe and compliant. By collecting, organizing, and regularly updating SDSs, you can ensure that your employees are always prepared for emergencies. Don’t forget to train your team and stay on top of compliance.
Our tool makes managing SDSs much easier, helping you focus on running your business while staying safe and compliant.